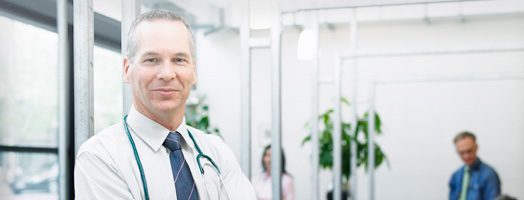
CASE STUDY: STREAMLINING A MEDICAL CREDENTIALING PROCESS
by Jan Bauer, Lean Six Sigma Master Black Belt
Medical credentialing is a precise, mandated process used to evaluate the qualifications and practice history of physicians, nurse practitioners and other health professionals. It is a crucial first step in recruiting and appointing qualified health care professionals to a facility.
Errors made in medical credentialing can result in harmful quality issues and damaged reputations. Likewise, the inability to quickly process individuals through the credentialing process can delay critical resources from being available to work in the facility. Inadequate patient care and poor patient experiences may result. This case study highlights how Lean Six Sigma was used to to improve the credentialing process, resulting in a streamlined process with reduced cycle times and performance that that now exceeds industry standards. Credentials are reviewed on a regular basis following standards established by states, regulatory bodies, and accrediting organizations. The three major accrediting organizations are the National Committee for Quality Assurance, the Joint Commission the Utilization Review Accreditation Commission, and, the main government agency, the Centers for Medicare and Medicaid Services. These independent, non-profit organizations set and regulate quality standards for healthcare organizations, credentialing organizations, and hospitals.
Credentialing involves the primary source verification of a healthcare practitioner’s education, training, work experience, licensure, etc. A variety of resources are used to verify the information including direct communication with educational and training institutions, past and current hospital affiliations and employers, peer reference letters, certification boards, licensing agencies and other sources. It is not unusual to find it necessary to make multiple attempts to obtain responses. These delays can be a major cause of long cycle times for this process. The industry average credentialing processing time is less than 90 days, with 60 days as a gold benchmark.
This project required strong change leadership skills. It is discouraging when the Lean Six Sigma Black Belts receive feedback such as, “This is not going to work!” Credentialing Specialists on the team voiced in unison that “cycle time was out of our control,” the primary verification process is “dictated” by Joint Commission, special demands to push packets through the process create havoc, and the reason for extended cycle times is that workers must constantly nag the primary sources for information.
However, just like any successful performance improvement project, there is a point when the team has a "eureka moment." In this case they realized that they are in control of the cycle time! Each complaint was tested against real, hard data. The team identified waste in the process and determined how to corral the requests for information from the primary sources, or as they stated, “design the process to be robust against demands.”

The 63% reduction in cycle time was the result of a collection of simple solutions that involved Lean tools and some good old-fashioned elbow grease. The team improved the flow by standardizing the process, eliminating several unnecessary quality inspection loops, applying visual management techniques such as color codes highlighting the status of all packets, and cross-training all credentialing specialists to ensure that each was able to credential any type of provider. A Failure Modes and Effects Analysis (FMEA) was developed that identified and prioritized the top five "red flag" situations that would short-circuit the credentialing process. Response plans were developed for those each of these conditions.
Follow Us: