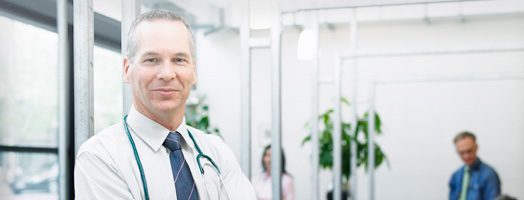
Case Studies
NOVACES has worked with various government organizations to assist with the deployment of Continuous Process Improvement (CPI) programs. The teams we have trained and supported along the way have improved important metrics related to military readiness and government service quality. Listed below are some examples of the results.
Invoice Payment Process Medical Claims Processing decreased a government agencies invoice processing time by 30 days and improved the erroneous payment rate by 80% for a large DOD organization. This improved budget accountability and improved vendor relations.
Security Clearance Process Improvement improved the cycle time by over 70% for the in-processing of new personnel for initial or add on security clearances. This project led to a productivity improvement of over 60 days for personnel requiring special clearances to begin work thereby accelerating the employee’s availability and improving project cost and schedule determinations.
Common Access Card (CAC) Processing decreased CAC processing cycle time for government employees from 19 days to 1 day. This was completed through a multi-department effort that led to significant residual improvements. For example, it increased employee utilization by having access to work files faster.
Reduction of Cycle Time for Memorandums Of Understanding reduced the cycle time to complete and certify MOUs from an average of 29 days to 14 days.
New Employee Check-in Procedures reduced the check-in time for contractors from 2 weeks to 2 hours and new civilian employee check-in was reduced from 2 weeks to 3 hours. Productivity was increased by approximately 7,680 man hours. Further savings were generated from departmental cross training that allows better check-in flow.
Annual Occupational Health Screening saved $504,000 annually. This project looked at the different reasons for missing the appropriate screening and identified incomplete occupational health screening as the root cause. The process steps were revised, standard work instructions updated and all appropriate personnel trained regularly on the new procedures.
Inventory Management for High Cost Immunizations produced a cost avoidance of $180,000 and savings of $41,980 by reducing database entry cycle time by 60%. This project was able to achieve savings and cost avoidance by identifying optimal order quantities, optimizing just-in-time supply chain deliveries and the capture of out dated immunizations using Reverse Distribution Contracts.
Credentialing Process for Physicians and Nurses reduced the credentialing cycle time for physicians at a pilot medical facility from an average of 38 to 27 days with an annualized savings of $477,000. Credentialing cycle time at the same facility for registered nurses was reduced from an average of 38 days to 20 days with annualized savings of $312,000. The newly revised processes for both physician and nurse credentialing rolled out to the entire medical system will generate an estimated savings of $114,000,000.
Source Selection Process Improvement generated an annual savings of $300,000 and over 80% improvement in cycle time for small- to mid-scale contracting actions. Removed non-value added steps and implemented standard operating procedures to streamline the actions of source selection authorities and contracts support.
Aircraft Engine Fuel Control Quality Improvement produced a benefit of $117,200 annually with a 90% improvement in repair cycle time. This project looked at the reasons for failures in engine components and the waste associated with the inspection, re-inspection and quality control. A supermarket approach was implemented to improve component availability and 160 non-value added steps were removed from the process greatly reducing the amount of labor required and improving the quality of the process. Standard work instructions updated and all appropriate personnel trained regularly on the new procedures.
Fuel Accountability Process Improvement provided an $11 million improvement in fuel cost variability. The project improved the quality of the reconciliation between allocated flying hours and the actual cost of aviation fuel. The project reduced the number of wasteful steps and “mistake proofed” the process to insure accuracy in the reporting mechanism. This process also reduced the labor required to operate the process by over 70% and greatly reduced the frustration associated with it.
Engineering Requirements Determination Process saved $400,000 annually in rework avoidance requiring unplanned labor and overtime. The rework associated with incorrect engineering requirements was reduced by 60%. This project was able to achieve the benefit by identifying the optimal process for the translation of customer needs and wants into actionable engineering requirements of high quality and purpose.
Follow Us: